The applied side in the science of industrial cost accounting :-
The importance of cost science, the objectives of cost science, the cost of raw materials as a major component of the production order cost, direct industrial costs, standard costs, standard costs, and deviations of industrial costs.
Mohamed Tohami - • Capital ERP for System Managment
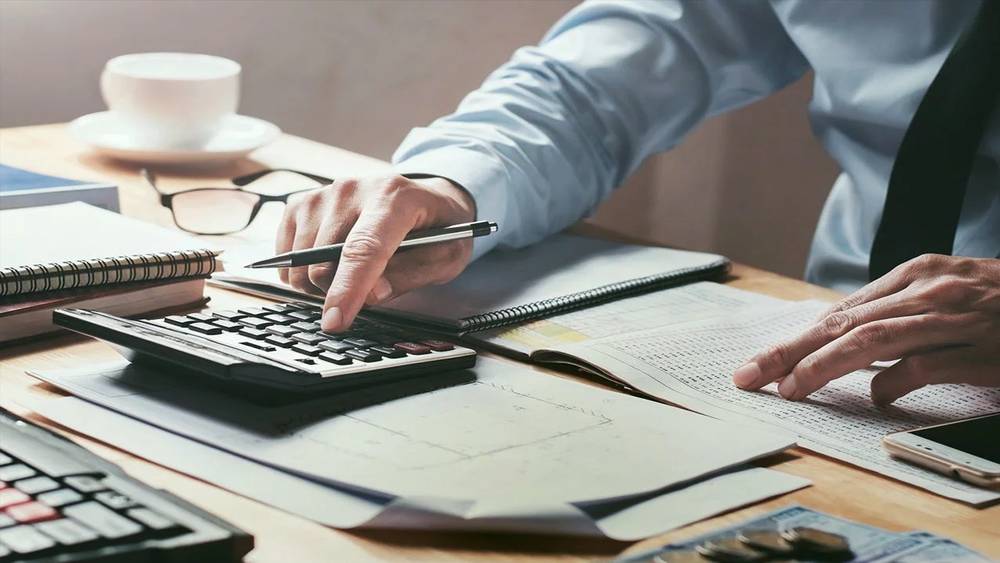
The applied aspect in the science of industrial cost accounting : -
CopyØ The importance of costing.
Ø Objectives of cost science.
Ø The cost of crude as a major component in the cost of the production order.
Ø Direct industrial costs (labor cost, direct wages, direct expenses and depreciation).
Ø Standard costs, types and objectives.
Ø Standard costs of indirect industrial costs.
Ø Deviations of indirect industrial costs and how to analyze them and equations.
Ø A comprehensive example of an integrated process case.
Objectives of Cost Accounting :-
CopyThe main and only cost accounting objective is to determine the cost of the unit produced or the service provided, as determining the cost helps to:
2- Take the appropriate decision to determine the selling price compared to the estimated or actual cost to make the appropriate decision, such as:
1- Determining the cost of inventory for complete and incomplete production for industrial companies and determining the profit compared to the selling price Determining the cost of operations under implementation deducted to meet the revenue with the extract.
2- Providing the necessary data for planning, where by determining the cost and the presence of accurate information that helps in planning better than inaccurate data that comes to the company with serious consequences for the company in need.
3- Assisting in achieving control and evaluating the performance of the facility, and this is done by comparing the actual cost with the estimated cost (standard) to determine the deviation as a first step to know the deviations in the cost and their causes, and thus develop measures for the correct performance of the standard cost after that.
4- Assisting in making administrative decisions, as it helps costs in making and rationalizing administrative decisions that are based on the trade-off between different alternatives to rationalize the cost and maximize profit .
Cost elements in the production order : -
CopyCost elements in the production order : -
CopyIncoming cost : -
• The cost of import, as in IAS 2, comes from the historical cost of inventory, i.e. all purchase costs, conversion costs, and other costs incurred in bringing the inventory to its current location and conditions.
• Includes cost from 3 sources.
• Standard 2 also mentioned the international standard that there are 4 expenses or cost sources that are not included in the cost of inventory, namely:
1-Storage cost unless such costs are necessary for production processes that precede another production phase .
2-Marketing, sales and administrative expenses .
3-Borrowing cost (financing expenses) .
4-The cost of perishable or damaged from raw or complete stock .
Exchange cost : -
CopyThe inventory is evaluated upon disbursement in 3 different ways :
1-The incoming first is spent first
2-Weighted average cost
3-Patch cost
Incoming first to be disbursed first : -
CopyIt is a method adopted when buying inventory in certain quantities and a certain value, the quantities received first exit at their cost and then the exit of the purchased products after that with their quantity and value, for example:
Weighted average cost :-
CopyThis method of evaluation was agreed upon by most experts and consultants because of its proximity to the practical reality of companies, where when the stock comes out of the stores, there is an impossibility on the inventory ground that the distinction is made for the same product with the same specifications and in one place, despite the purchase of the same product at two different prices, and therefore the solution came in the weighted average so that a calculation is made in the inventory through which the cost of inventory is calculated with the total cost of inventory on the total quantities:
Total stock value (20+24)
-----------------------------= (11) average cost
Total quantities in warehouses (2+2)
Patch cost : -
CopyIt is the cost derived from the cost of the import first disbursed first, but with different standards, where in the patch what is produced or purchased at a certain cost with certain specifications with a certain composition of the product becomes adjacent to it until it is sold (the patch is pasted on the product)
• Where the item information for the patch is recorded on the product and therefore when it is returned from the market and found if it has specific defects in this patch and this example is more evident in pharmaceutical companies and food companies, which facilitates the knowledge of the defects of each patch and thus easy collection from the market through the patch that has the defect and adjust its defect and reproduce it again.
• Or determine the amount of sales of each patch for the same item and thus monitor the quality of the product and its impact on the market and the ability to measure its quality such as the automotive industry.
Practical difficulties in calculating the cost of ore : -
Copy1- The administration adheres to the use of a specific method of cost calculation that is not commensurate with its activity.
2- Delay in the receipt of purchase documents, whether import or local, and therefore must be verified: - The ability of the current system or internal control to put a temporary cost until the arrival of purchase documents and not to allow the existence of zero cost of inventory.
• After feeding the necessary purchase documents for the inventory, can the current system recalculate the operations that took place before that and affect the chart of accounts or not.
3 - The establishment obtained a bonus at the end of the year, which results in a decrease in the cost of inventory, despite the loading of the previous cost before the bonus on production orders or sale
4 - Not to separate the raw materials of the trusts in an account or a special item away from the products or raw materials with a cost in stock.
Practical case on the disbursement of raw materials :-
CopyA production order (work order) was opened for product X in the amount of 100 units, raw materials worth 1000 EGP and packaging worth 500 EGP were disbursed.
How much is the share of each unit of ore by production order and the work of the necessary restrictions.
1000 (raw materials)+500 (packaging)
Unit share of raw materials and packaging =-----------------------= 15 g per unit
100 Units
2- Direct industrial costs : -
Copy• They are the costs closely associated with the product and are intended for this product and not for others.
•As:-
1-Direct wages.
2-Depreciation allocated to the production line for a specific product.
3-Direct expenses (electricity, gas ......) allocated to the production line
(2-1) Labor cost and direct wages :-
Copy- It is the cost of the worker's wage associated with the machine (production line) directly related to the production of a specific product on a specific production order.
2. The cost of wages and direct labor is considered one of the costs depleted, i.e. the actual costs that are spent and charged on the production order directly.
3- The mechanism of monitoring the labor element in the industrial facility is done by recording the actual time where the workers are present on the machines or production lines, on the basis of which the worker's time is calculated and therefore
Determining his wages.
Time Sheet (production card for workers) :-
Copy- We note here in the Time Sheet for workers the presence of the name of the worker, the production line or machine that has been worked on, the product charged with the cost, the amount of production in each batch or the quantity supplied, and the number of hours taken to produce the necessary units.
2- Calculating the share of the production order from the cost of wages = actual hourly wage rate x number of actual operating hours x number of workers on the machine (production line).
- We note here in the Time Sheet for workers the presence of the name of the worker, the production line or machine that has been worked on, the product charged with the cost, the amount of production in each batch or the quantity supplied, and the number of hours taken to produce the necessary units.
2- Calculating the share of the production order from the cost of wages = actual hourly wage rate x number of actual operating hours x number of workers on the machine (production line).
Wage per worker per day =----------=---------= 200 EGP \ number of days in the month 30
200 (per day wage for a worker)
Hourly wage =------------------------------------ = 25 EGP per hour
8 (number of working hours)
Production order share of wage cost = 25 (hourly wage rate per worker) X 6 (number of hours of operation for the order) X 2 (number of workers) = 300 EGP
300 share of unit X of wages by production order =--------------= 3 pounds. 100
Necessary restrictions:-
Copy(2-2) Other direct expenses:-
CopyThe most famous of them is electricity and gas, where many factories have the ability to allocate any of them on a specific production line for the benefit of a specific product, and in this case the expense will be treated as a direct expense, meaning that (each increase in the number of production is followed by an increase in the expense)
In the event of inability to find the relationship referred to above, these expenses will be treated as indirect expenses and therefore included in the cost of the product at a chargeable rate (estimated)
(3-2) Direct Depreciation:-
Copy• It is the calculation of the depreciation of machines or related production lines, i.e. the allocation of depreciation on a specific product
• In the event of inability to find the relationship referred to above, these expenses will be treated as indirect expenses and therefore included in the cost of the product at a chargeable rate (estimated
Practical difficulties in calculating direct wages in practice: -
Copy1- The lack of time sheet in the companies for the workers on the production lines and therefore the lack of knowledge of the time spent in the production of the product and therefore forced cost management company to make time and cost standard time spent for the production order.
2- The lack of a sound human resources system in the facility leads to the failure to calculate wages correctly.
3 - In the presence of the current technological progress, there must be a strong system in the facility that allows the recalculation of the cost of wages for production orders when there is a deviation between the standard and the actual rate
4- The inability of the system and the difficulty of calculating the cost of additional time for the worker during the production process and loading him on the production order.
• Standard costs: -
CopyDefined:
• It is the estimated cost of a product, which the facility can measure on one product and is based on a study of the cost of future expenses of the elements involved in production according to the economic conditions and the environment surrounding the facility and analysis of deviations resulting from this cost with the actual cost.
•Objectives:
Determine the standard unit cost of production before operation and thus determine the deviation between the standard and actual cost.
Assist the management in planning and the availability of information necessary for the production of the future unit.
Assist the administration in trying to overcome the obstacles that may face production and disrupt it in the future
Assist management in pricing products (selling price) based on cost (standard costs with direct costs) of the product until the actual cost occurs, compared and adjusted.
Types of standards and their methods : -
Copy• First: The types of standards that must be taken into account when determining the standard cost of the product, namely: -
1-Ideal standards.
2-Natural standards.
3-Expected standards.
• Second: Special methods for determining the standard cost: -
1-The historical method of the product
2-Experimental method of the product
3-The realistic way of the product
First: The types of standards that must be taken into account when determining the standard cost of the product, namely: -
CopyIdeal Criteria:-
These standards are based on what is expected to be produced in the future at the maximum level of operation under ideal conditions of production (in the absence of machinery breakdown or delay of workers to produce the unit), meaning that the facility uses its production capacity by 100%.
Natural Parameters:-
They are the standards based on what is expected to be produced in the future in the presence of a deviation allowed under the normal conditions of the facility and taking into account the expected circumstances of machinery breakdown, delay of workers, power outages or ...... etc., but with specific criteria
Expected Criteria:
They are the criteria based on what is expected to be produced in the future in light of a previous study of what happened with the facility previously of deviations in the presence of the state of the facility as it was in the past with minor deviations, if any.
Second: Special methods for determining the standard cost: -
Copy1. The historical method of the product: -
CopyThis method depends on the historical data of the production of the product and thus knowing the costs charged from previous periods and making an average share of the unit of production for each expense according to the importance of the expense for the facility and the rest is done at the expense of other loaded expenses.
But there are some disadvantages in this way, which is taking into account what happened in the past of censorship or lack thereof and historical events that may not be repeated in the future.
2. Experimental method of the product: -
This method depends on the experiment, i.e. the experience of producing a sample of each product separately in specific quantities and measuring the time period and expenses necessary for its production and thus setting standards for the production of quantities corresponding to the quantities of the experiment and submitting a report for production in these quantities authorized in light of the experiment.
Disadvantages Exhaustion of production capacity to conduct an experiment once, twice, or even three times with the inability of the facility to measure expenses and lack of experience to calibrate quantities correctly and thus give false information to production.
3- The realistic method of the product: -
It is a method that depends on historical data, but it is taken into account what happens in the future from the purchase of assets, for example, which saves time and increase production and thus reduce the cost of hours in production and also face the events that affected the increase in the cost of production for previous periods and take the necessary measures to confront these problems and punish the culprit and choose the lowest cost during previous periods and take it into account as a cost criterion for expenses in the standard cost.
They are all the elements of costs that enter into production or to facilitate the production process and are not part of the components of production, which are not directly related to the production order or the productive unit, such as indirect wages such as supervisors of production workers or other indirect expenses such as rents, electricity that is not present on the production line, gas, water, etc.
Difficulties of measuring indirect industrial costs: -
Copy1- The nature of the expense as it is a general expense that cannot be determined on a specific production order or a specific product.
2- The nature of the heterogeneous expense as well, as it is affected by the volume of activity from an increase or decrease, such as increasing the area of the factory and thus affecting the expense of electricity and its consumption, or there are general items such as rent also from an increase and thus an increase in cost.
3- The small indirect industrial costs in relation to the direct costs make them of second or less importance for the decision maker.
Calculation of the rate of indirect industrial costs charged: -
CopyStandard Indirect Industrial Costs = Number of hours of actual production X Standard rate of chargeback
And the restriction shall be ....... H/ Stock under operation
........ H/ Standard indirect industrial costs
How to measure deviation in indirect industrial costs charged: -
CopyThe deviations of the standard indirect industrial costs are determined by comparing them with the actual indirect industrial costs in the trial balance, as the nature of the standard or loaded expense is creditor and the actual expense is debited, as they meet in the balance, for example, as follows:
Deviation in indirect industrial costs = actual indirect industrial costs - standard indirect industrial costs
The following is the form of the balance in the presence of indirect industrial costs charged and actual indirect industrial costs.
For our services, click here
To request a demo of the Capital ERP system, click here